Você sabia que o processo de pintura eletroforética é derivado do processo de fabricação de luvas cirúrgicas e camisas de Vênus, criado no início do século XX?
Todos os artigos de admin
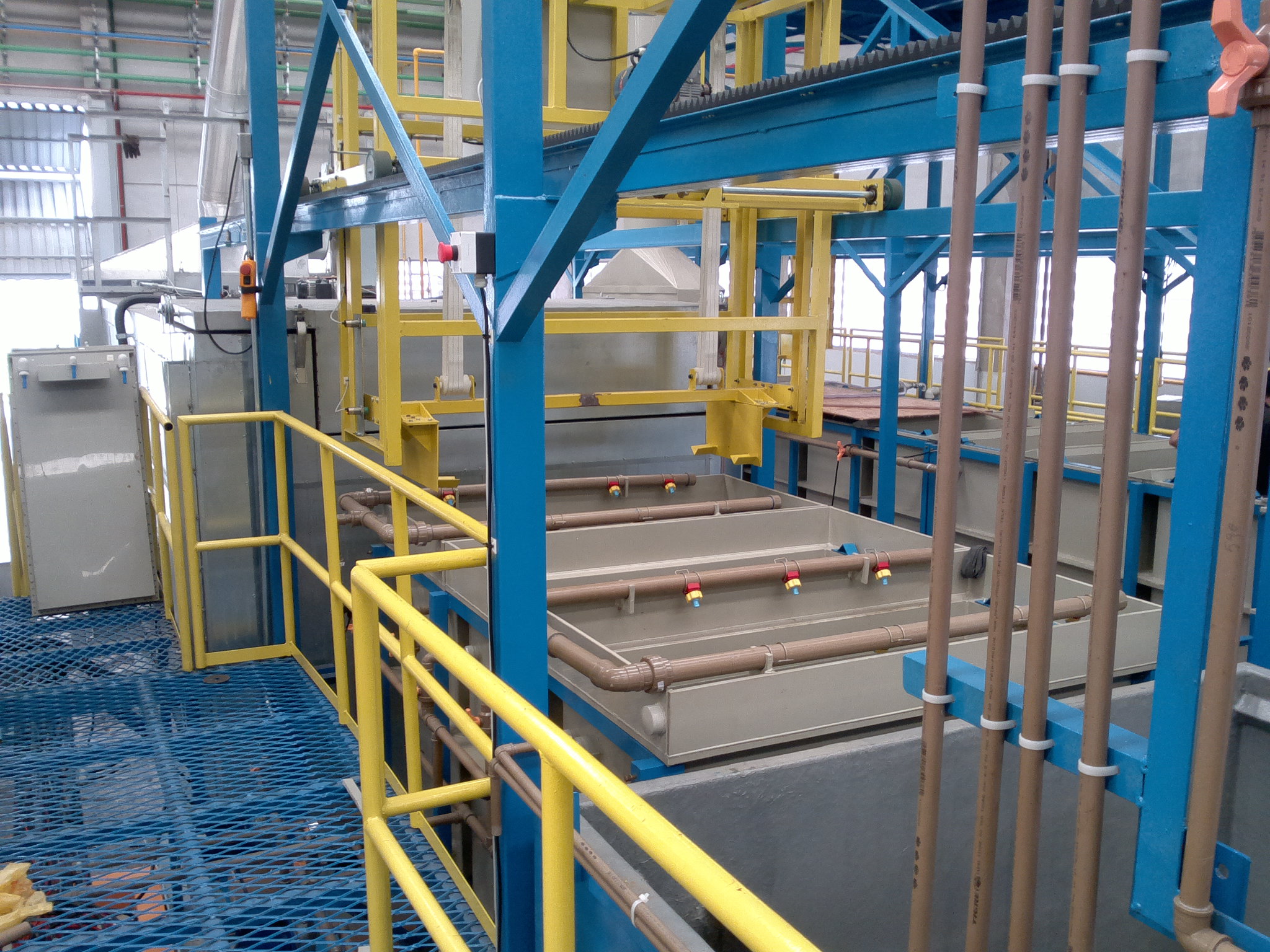
A IMPORTÂNCIA DO ESCORRIMENTO (DRENAGEM) EM PROCESSOS DE PRÉ-TRATAMENTO
Muita gente em nossa indústria (pré-tratamento e pintura) não enxerga a importância do processo de drenagem ou escorrimento de peças durante os processos de pré-tratamento e pintura.
Nos casos de sistemas de transporte contínuo, o tempo de drenagem, além de agregar tempo ao processo como um todo, agrega comprimento ao equipamento e, por consequência, maiores investimentos, seja no túnel, seja no transportador.
De um modo geral esse tempo de drenagem é desprezado por operadores e mesmo por alguns projetistas de equipamentos (de baixa qualidade digamos de passagem) pelo fato de não o considerarem propriamente um processo.
Mas é sim um processo! Coisa que poucos enxergam.
O processo de drenagem é de suma importância para evitar problemas de carregamento e contaminação cruzada entre estágios, além de marcas de superfície (revelação) entre outros problemas.
Em sistemas manuais ou mesmo em sistemas automáticos por bateladas, os tempos de drenagem são infelizmente mais desprezados ainda, porque em alguns casos é visto como tempo “morto” que reduziria a produtividade do sistema ou também por vezes o excesso de líquido é enviado para o sistema de tratamento de efluentes, fazendo com que o operador veja tal processo como um “desperdício”. Em muitos sistemas o retorno deste líquido é feito ao estágio de enxágue do qual as peças foram retiradas, e neste então é feito o controle de concentração do produto sendo enxaguado, com reposição para a manutenção de níveis adequados de tal concentração.
Os processos químicos para obterem resultado demandam uma relação adequada entre tempo de ação, temperatura e concentração. Os enxágues devem ser feitos com água cujas concentrações dos produtos enxaguados estejam dentro dos níveis adequados ao processo e por isso demandam renovação. Muitas vezes é usada água limpa (água industrial, água de osmose reversa, água DI, e assim por diante) principalmente ao final de processos críticos ou ao final de ciclos completos.
E qual o papel na contaminação cruzada?
Quando temos os enxágues contaminados o resultado final é ruim pois estes permitem muitas vezes que o próximo processo a ser executado corretamente ou por que contaminam o próximo estágio, exigindo trocas e reposições mais frequentes e por consequência maiores custos e menor eficiência do sistema.
Tudo em um sistema deve ser projetado para fornecer o melhor resultado final que você e seu cliente tenha considerado importante, ou um compromisso entre o que deve ser melhor e o que é possível fazer com os recursos disponíveis, porém nunca abaixo do que o cliente final necessita.
Por vezes (quase sempre) os projetistas e engenheiros de equipamentos de pré-tratamento e pintura são levados a economizar em todas as partes do projeto, os orçamentos são restritos e devem ser respeitados ao máximo possível.
O mais comum de se ver é a tentativa de eliminar ou reduzir aquilo que muitos consideram “tempos mortos”.
Não devemos fazer isso com as drenagens / escorrimentos antes de analisarmos profundamente o caso para toda a gama de peças a serem tratadas.
Outros motivos para estudarmos melhor os espaços de escorrimento / drenagem:
Uma outra necessidade dos espaços entre estágios, no caso de sistemas de transporte contínuo, é por causa de respingos e do “efeito duto” (a peça forma um duto entre o estágio do qual está saindo e o estágio seguinte). Por causa destes dois possíveis efeitos devemos tomar mais cuidado ainda e sempre favorecer os intervalos de escorrimento.
Por vezes é impossível somente com espaço entre estágios evitar os respingos, ou porque a limitação de espaço impede que se faça tais estágios longos o suficiente ou porque o tempo se tornaria longo demais, secando a peça e assim trazendo novos problemas.
Se fizermos um estágio de escorrimento muito longo corremos o risco de secar as peças, e como exposto acima, gerar novos problemas no tratamento de superfície. Por vezes, para peças muito longas ou com muita retenção, os tempos devem ser efetivamente muito longos, restando então a colocação de sprays tipo névoa, com uso de água deionizada ou para processos menos críticos somente água limpa, em regiões adequadas para manter a superfície das peças úmidas.
É possível supor a partir de análises teóricos ou extrapolação de dados práticos de casos diversos, quais seria os tempos de escorrimento das peças, quanto de material de arraste é levado ao estágio seguinte conforme o tempo é aumentado, entre outras coisas, e assim determinar o ponto “ótimo” onde se pode ter o encontro da necessidade com a possibilidade.
Mas a melhor opção é certificar-se de pendurar suas peças ou semelhantes e fazer testes de drenagem, exaustivos até, para determinar estatisticamente os tempos necessários, verificando o caso real de como a água drena em ambas as direções e quão longe ele “resvala” ou é conduzida quando em processo.
Desenha-se então o “estágio” de drenagem para capturar esta água para que os parâmetros de processo permaneçam com a menor alteração possível.
O que mais pode ser feito?
Outra solução, para os casos de estágios curtos por falta de espaço seria a utilização de sopro “contra corrente” com bicos de alta velocidade ou facas de ar.
Como encaminhar a solução do problema?
Um conceito pouco disseminado é o de que para um bom acabamento a coisa mais importante é uma boa limpeza superficial. A aplicação do fosfato ou nano componentes que gerem selagem e ancoragem da tinta à peça não acontecem de forma adequada se a peça estiver suja, com resíduos graxos, por isso devemos dar importância máxima à limpeza das peças.
Existem muito métodos, de sistemas com vapores solventes a conversores de óleos, mas a limpeza das peças sempre será o ponto de entrada de um sistema de pré-tratamento e o resultado será altamente dependente de se utilizar um processo de limpeza com enxágues adequados.
O mais alto desempenho dos revestimentos e pré-tratamento se dão a partir do uso de processos de limpeza aquosas, porém existem processos “a seco”.
Do sistema de lavagem manual de alta pressão, aos sistemas por spray e imersão, complexos e automatizados, a definição deve vir sempre do fabricante dos produtos químicos de forma a coincidir com os requisitos especificados pelo cliente final, o fornecedor do equipamento pode sempre construir o sistema de pré-tratamento adequado, pode propor alterações e inovações, mas sempre deve estar em consonância com os fabricantes dos produtos químicos de pré-tratamento.
O que preciso informar?
Vários fornecedores podem ajudá-lo a determinar qual o melhor processo para seu caso, a partir das seguintes informações:
• Definir a exigência de acabamento – normas do cliente final, horas de testes de corrosão, Padrão de adesão, tipo de utilização (interior ou exterior).
• Definir o tipo de revestimento: revestimento à base de água (requer limpeza excelente), revestimento a pó (requer limpeza excelente) ou tintas à base de solvente ou revestimentos (ligeiramente mais indulgente com gorduras nas superfícies).
• Orçamento disponível, apesar de a decisão dever ser com base na qualidade, sempre deve-se ter a noção do equilíbrio e de até onde se pode chegar com o investimento em equipamento.
• Quantidade de peças a ser produzida: Se for baixa produção permite mais flexibilidade, enquanto alta produção pode ser muito mais rígido e consequentemente mais caro.
• Área disponível para estes processos.
• Outras limitações (cronogramas, prazos de entrega, tempos em produção, etc.)
Precisa de ajuda para definir seus futuros processos ou para avaliar processos existentes?
Precisa de ajuda para projetos ou definições iniciais (linhas gerais, descritivos para orçamentos, etc.)?
Podemos ajuda-lo, consulte-nos!
Estamos à disposição no telefone 11-3280-7990, através do formulário abaixo:
[contact-form to=’vendas@addcor.com.br’ subject=’BLOG E-COAT – DRENAGEM’][contact-field label=’Nome’ type=’name’ required=’1’/][contact-field label=’Email’ type=’email’ required=’1’/][contact-field label=’Website’ type=’url’/][contact-field label=’Comentário’ type=’textarea’ required=’1’/][/contact-form]
Ou pelo e-mail: vendas@addcor.com.br
CÉLULAS DE DIÁLISE
Porque e onde as células tipo caixa são melhores que as tubulares?
Bom, esta é uma pergunta que pode parecer estranha para muitos daqueles que são usuários ou projetistas de sistemas de pintura e-coat (KTL), mas é a pura realidade.
Neste primeiro post vamos discorrer sobre algumas vantagens simples das células planas ou caixão sobre as tubulares, em posts subsequentes vamos aprofundar a respeito de onde cada tipo de célula é melhor utilizada.
Vantagens das células planas:
1. São extremamente mais baratas.
a. O custo das células planas ou caixão é cerca de 50% do custo da tubular de mesma área nominal.
b. Para uma mesma área nominal, a área efetiva da célula plana é entre 30% e 40% maior que a área de célula tubular.
2. São fabricadas no Brasil com tecnologia brasileira
a. Dão empregos a brasileiros
b. Em caso de problemas é mais fácil recorrer ao fabricante e obter a troca, fora o fato de que as células importadas a garantia nunca cobre a parte alfandegária e custos de transporte, ou seja a garantia das células tubulares é na verdade parcial.
3. Oferecem uma gama muito grande de variações de medidas (altura x largura) podendo ir de células para sistemas de laboratório (algo como 250 x 200 mm) e chegar a 3 metros de comprimento por 1 metro de largura.
Antigamente se dizia que as células tubulares tinham a vantagem da manutenção mais fácil, pois os eletrodos eram removíveis com facilidade e não era necessário se retirar as células do tanque para se fazer manutenção nos eletrodos.
Hoje porém, desde 2002, após desenvolvimento que se iniciou em 1999, a Add Cor fabrica células “OT” (Open Top), além de cópias inferiores feitas por alguns de nossos concorrentes, onde é possível retirar o eletrodo para inspeção ou troca sem a necessidade de se retirar a célula do tanque, o que elimina a “grande vantagem” que as tubulares tinham.
Pense nisso: da próxima vez que pensar em células de diálise, considere células planas.
Entre em contato, envie sua mensagem, estamos prontos para auxiliar na escolha do produto mais adequado para seu processo de pintura e-coat.
Preencha o formulário abaixo que entraremos em contato.
[contact-form][contact-field label=’Nome’ type=’name’ required=’1’/][contact-field label=’Email’ type=’email’ required=’1’/][contact-field label=’Website’ type=’url’/][contact-field label=’Mensagem’ type=’textarea’/][/contact-form]
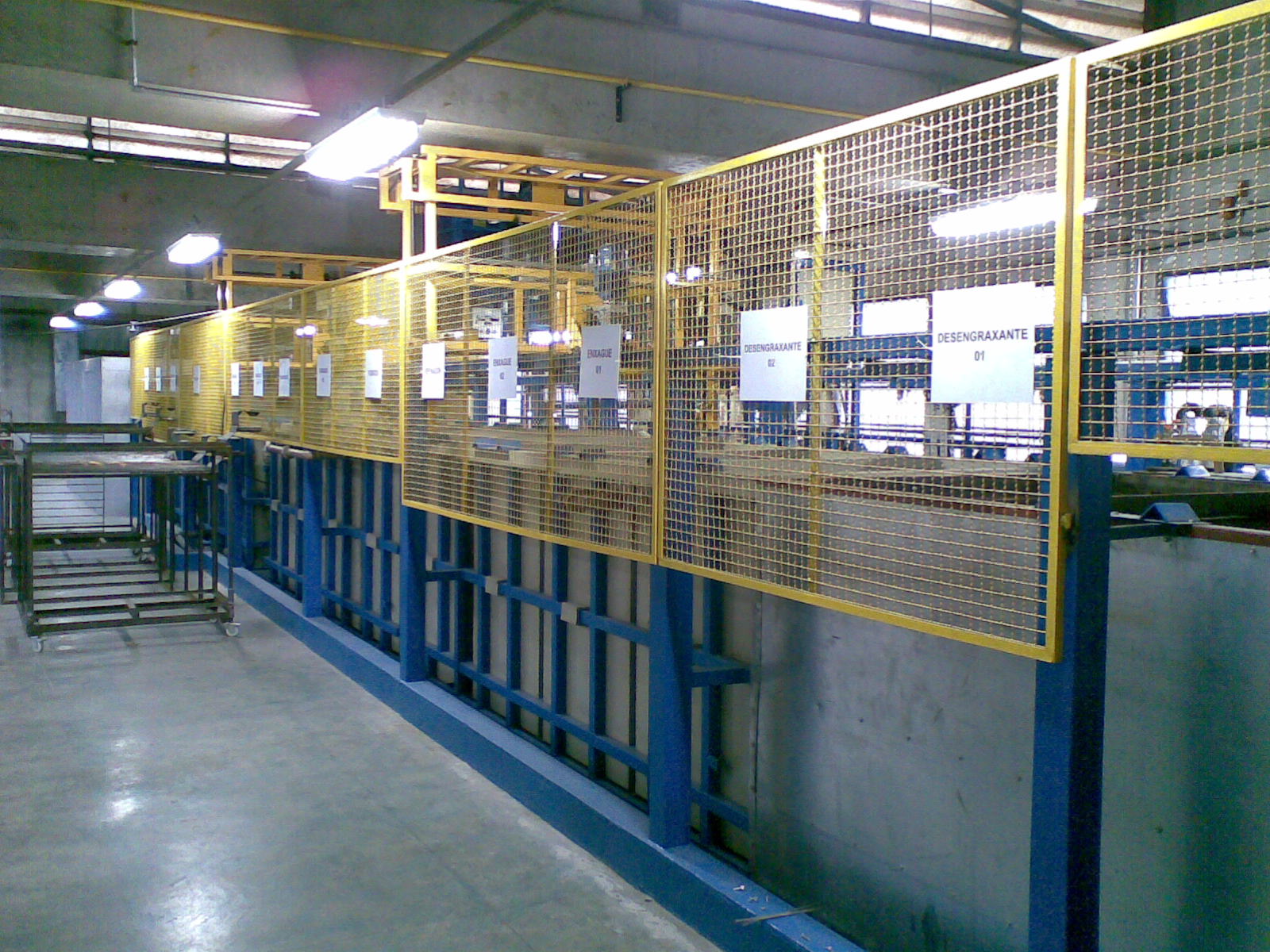
O QUE É ELETROFORESE (E-COAT / KTL)?
Parte do texto abaixo é baseado em informações contidas em apostila escrita pelo engenheiro químico Nilo Martire Neto há muitos anos, sendo ainda uma das melhores referências em português referente a este assunto.
Os primeiros processos industriais de eletroforese foram desenvolvidos para se criar camadas muito finas em látex de borracha.
Inicialmente, ainda na primeira década do século 20 este processo foi utilizado para a confecção de luvas cirúrgicas e materiais afins.
No final dos anos 50 iniciaram as pesquisas visando utilizar este processo para a proteção superficial.
Uma confusão muito grande é tratar os processos de pintura por eletroforese como se fossem processos de galvanização.
Outro problema comum (principalmente quando se consulta a internet) é encontrar muitas referências a processos de eletroforese e equipamentos para a elaboração de testes de DNA ao invés de para processos de pintura.
Nos testes de DNA as proteínas migram entre os eletrodos e se depositam conforme seu tipo, gerando ao final a figura que determina o perfil genético, enquanto na pintura por eletroforese a tinta migra e se deposita gerando proteção superficial. As tensões aplicadas, tamanhos, tipos e potências dos equipamentos não têm nada a ver um com o outro.
A pintura por eletroforese como processo de pintura foi desenvolvida para atender aos requisitos anti corrosivos exigidos pela indústria automobilística, de autopeças e de eletrodomésticos.
A pintura por eletroforese desde então passou a ser conhecida por muitos nomes, alguns a chamam de “elpo” (de eletro deposição), outros de “e-coat” (do inglês electro coating), ou “electrodip”, “electropaint”, “paint plating”, “eletrodeposição”, “pintura eletroforética”, “AED”, “CED”, “HFBEC”, “LFBEC”, “KTL” e “DKTL”.
Basicamente, a eletroforese ocorre quando se mergulha um corpo metálico em um banho de tinta especial para tal processo, normalmente diluída em água, e se faz passar uma corrente elétrica, tendo a peça conectada a um pólo e o outro pólo conectado aos eletrodos.
Pela teoria, quatro fenômenos ocorrerão durante o processo de pintura:
1. ELETRÓLISE:
É o fenômeno proveniente da reação de óxido-redução onde ocorre a separação de íons, isto é, hidrogênio e
oxigênio, em solução, sob a aplicação de uma diferença de potencial elétrico.
b. ELETROFORESE:
E o fenômeno de migração da partícula de pigmento, envolvida pela respectiva resina e
demais componentes da tinta, em direção a peça a ser pintada, quando a mesmo é
submetida a uma tensão (diferença de potencial) elétrica.
c. ELETRO COAGULAÇÃO:
Basicamente, o que ocorre neste fenômeno é a aproximação do macroíon ao pólo contrário a
sua carga, onde há uma troca de carga elétrica, provocando a adesão da partícula ao
substrato, formando assim um filme de tinta insolúvel em meio aquoso.
d. ELETRO OSMOSE:
E o fenômeno de eliminação dos eletrólitos contidos no veículo da tinta aplicado, onde o material eletrodepositado perde quase toda a água, tornando-se hidrófobo.
Alguns fatores determinam a espessura de camada: Tempo de aplicação (quem tem limites devido à assintoticidade do processo), diferença de potencial (Tensão elétrica), tipo de tinta, teor de sólidos, temperatura da tinta, entre outros.
Uma vez formado o filme, deve-se então passar por uma reação de reticulação, a qual ocorre com a aplicação de temperatura sobre o mesmo, sendo por isso necessário que se tenha uma estufa ao final do processo.
essa reticulação normalmente ocorre dentro do que chamamos a “janela de cura” ou seja, quanto mais alta a temperatura (dentro de certos limites) menor o tempo necessário para a reticulação.
Normalmente se trabalha com temperaturas que vão de 170 a 210° C e tempos em estufa que vão de 15 a 40 minutos.
Até 30% em Economia de Tinta
A Controlled Power junto com a Add Cor apresentam no Brasil o AACD, Automatic Average Current Density (Sistema Automático de Controle da Densidade Média de Corrente).
O controle da densidade de corrente é o que otimiza a uniformidade de camada na aplicação da eletroforese, fazendo assim com que não seja necessário pintar com margens de segurança muito grandes, economizando boa parte da tinta hoje aplicada.
O sistema regula automaticamente a tensão de trabalho de acordo com a carga que entra no tanque de KTL reduzindo as variações de espessura de camada, economizando até 30% da tinta utilizada (normalmente entre 10 e 15%).
O sistema é de fácil operação, dotado de IHM e PLC próprios para permitir a fácil programação do equipamento.
De um modo geral o sistema tem o retorno de investimento em algo pouco acima de um ano. Existem casos nos quais o retorno é inferior a um ano.
Pode-se também implementar no sistema o controle individual de células de diálise, aumentando ainda mais seu controle sobre a aplicação.
Revenda e Assistência no Brasil: Add Cor Engenharia – (11) 3280-7990
Contato: vendas@addcor.com.br
Veja a apresentação: “Economize Tinta”, um estudo de caso e um video mosntrando os resultados: https://drive.google.com/file/d/0B2z5ys87h8asZzhwYndvRkdkSVk/view?usp=sharing
https://drive.google.com/file/d/0B2z5ys87h8asUHZZQ2FXUzF2NXc/view?usp=sharing
https://drive.google.com/file/d/0B2z5ys87h8asUnhoU0U0a0NQams/view?usp=sharing
[contact-form][contact-field label=’Nome’ type=’name’ required=’1’/][contact-field label=’Email’ type=’email’ required=’1’/][contact-field label=’Website’ type=’url’/][contact-field label=’Comentário’ type=’textarea’ required=’1’/][/contact-form]
Estufas
Muitos não sabem ou simplesmente negligenciam a importância das estufas no processo de pintura e-coat.
Em termos de importância sabemos que cada parte tem seu papel, mas a boa distribuição de temperatura dentro das estufas é fundamental para um bom acabamento, uniformidade de resultado e resitência à corrosão.
Podemos tratar o tema por várias óticas, como a das janelas de cura por exemplo: A priori se ao se passar o termógafo 100% das peças estão dentro da janela de cura não teríamos com o que nos preocupar. Mas isso não é bem assim.
Outra forma de analisar o problema é respeitando a “linha de temperatura mínima”, que diria que se tivermos as peças por tempo suficiente dentro da estufa, acima daquela temperatura teríamos um bom resultado.
Existe ainda quem parâmetros como os da DATAPAQ para definir a qualidade da cura, o que se aproxima um pouco mais da realidade mas ainda assim comete excessos em alguns aspectos.
Por fim os mais antigos levam em conta um conjunto de dados muito simples e que de um modo geral funciona que é algo simples e que se aqueles que projetam e fabricam estufas seguirem tenho certeza que 90% do problema de cura estaria se não resolvido, reduzido. E o que é esse “método dos antigos”? Primeiro respeitar a boa distribuição das temperaturas para assim não termos possibilidade de sobre-cura ou sub-cura, ou seja a peça cura por inteiro ou a peça não cura por inteiro. Daí a segunda coisa é respeitar a linha de temperatura mínima por tempo (mínimo e máximo) que seria algo próximo ao método da “janela de cura”.
Em sua grande maioria os fabricantes de estufas não se preocupam com isso. Chegam por vezes ao absurdo de propor o uso de estufas de cura de tinta a pó para o processo de KTL que é muito mais sensível, ou de fazer estufas onde não se consegue regular o fluxo de ar que incide sobre as peças.
Outro problema sério que vemos são as estufas com baixa circulação de ar pois em primeiro lugar existe uma circulação mínima a ser respeitada, várias vezes superior à que se usa em estufa de cura de pintura a pó, e em segundo porque com uma circulação maior se pode obter melhor distribuição e controle do ar e das temperaturas.
Podemos ainda citar um sem número de estufas que não têm filtração no fluxo de recirculação levando sujeira a ser depositada sobre as peças.
Por fim podemos abrodar vários desses temas, deixo a vocês leitores e participantes que ou peçam ou os abordem a partir de sua própria experiência ou problemas que tenhma ou estejam passando.
ULTRAFILTRAÇÃO
DEFINICOES SOBRE ULTRAFILTRACÃO
a. O Que é Ultrafiltração
A definição de um processo de filtração, ultrafiltração ou microfiltração, depende das dimensões das partículas que o dispositivo em questão permite passar.
• A filtração vai de 0,1 a 1 micron , a ultrafiltração de 20 a 50 Å e a osmose reversa de 1 a 20Å
• Na ultrafiltração o elemento filtrante é uma membrana semi permeável, plana, tubular ou espiral.
• As técnicas de membrana permitem a eliminação de efluentes líquidos, bem como as suas recuperações.
• A retenção por ultrafiltração se efetiva a nível molecular.
• Só é possível se obter moléculas com peso molecular menor que um certo valor (normalmente macromoléculas) , passando pelas membranas.
• O tamanho das moléculas retidas depende da natureza das membranas, e, em certos casos e mesmo possíveis associações moleculares entre os componentes do soluto.
• A ultrafiltração tem uma relação muito grande com a osmose inversa, pois ambas necessitam de agitação na interface fluido/membrana, limitando a polarização do concentrado. Para tanto observa-se que a recirculação do fluido temos elevada velocidade.
Valores Práticos em Ultrafiltração em Instalações de Pintura por Eletroforese
Da pratica se obtém alguns valores de grande utilidade para estudos de viabilidade ou anteprojetos de equipamentos:
• Quantidade de Tinta recuperada por Enxágüe com U. F.:
9 g/m² (de superfície pintada)
• Quantidade de UF. Utilizado para o Enxágüe:
1,0 l/m² (Europa)
0,3 l/m² (Japão, porem com um investimento superior em tanques)
-
• Vazão Média de UF.:
20 a 35 l /m2h
Hoje se utiliza entre 1,5 e 2,0 l/m² para circuitos fechados onde não se usa água deionizada.
Olá!
Seja bem-vindo ao nosso blog!
Por acidente perdemos todos os artigos e discussões dos últimos 2 anos, daí aproveitei para dar uma reformada no Blog.
Mande seus comentários e dúvidas!